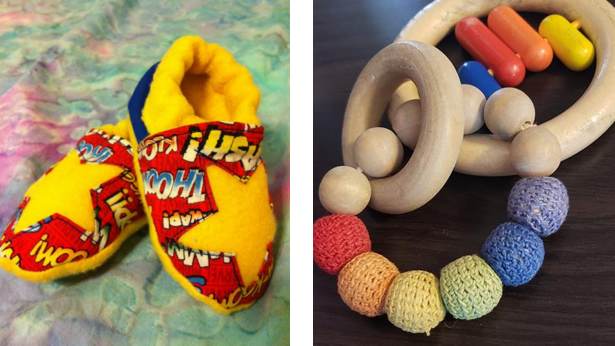
Among the many legal issues facing small businesses is consumer product safety compliance. In the United States, the Consumer Product Safety Commission (CPSC) regulates how products such as children’s toys and textiles are manufactured, labeled, and tested for safety.
Misty of Misty Henry Product Safety and Consulting Services, LLC teaches artisans and small business owners how to officially say, “Meets CPSC Safety Requirements” by helping them navigate the requirements surrounding labeling, testing, tracking, and record keeping. Her favorite part of what she does is brainstorming about an artist’s new designs and what safety concerns they may come up against.
What is consumer product safety compliance, anyway, and what should you know if you’re selling physical products? We interviewed Misty, and she shares some of her knowledge below.
What type of businesses need to register with the CPSC?
All businesses that create or import a consumer product should register at SaferProducts.gov. This website is the contact point for any safety concerns that may come up.
While you can report without registration, the online portal makes it more streamlined. Safety concerns submitted to you from your consumers should be reported within 24 hours and investigated immediately. Safety concerns submitted to the CPSC will be sent to you through your account and/or email linked to the account.
There is a secondary registration that is for qualifying small-batch manufacturers. These are businesses that create or have created for them, less than 7,500 units of any given product per year or gross, in total, under $1 million (the exact dollar amount is on the Safer Products website and may change year to year).
At what stage of business should a new business owner begin looking into consumer product safety compliance?
The brainstorming stage is best. Because much of compliance is based on the components of the products as much as the product itself, it is a good idea to at least start looking into what safety compliance is and what it means for your chosen product lines.
Think of it this way, would you rather purchase a ton of flannel to use for scarves and clothing just to find out that you need to send them in for flammability testing yourself, or would you rather know that need ahead of time so you can search for suppliers that already have the testing?
For weekly tips like this, subscribe to our newsletter
"*" indicates required fields
What are the risks of not registering with the CPSC?
Registration is actually optional as long as you are able to still report your safety issues within 24 hours of receiving notification of an issue. Registration is free and if you never end up making or importing a CPSC-regulated product, then it doesn’t hurt you at all; you just let it expire at the end of the year. Registration, though, is also what allows a small batch manufacturer to utilize some testing reports on components to limit or eliminate the need to test their own products for things like lead, flammability, and phthalates (BPA).
Legally, there are financial risks to not being compliant with the regulations. The fine amount can be in the thousands per violation depending on the circumstance and situation. There is also the financial risk should an injury occur. Between the CPSC investigation and the potential for court and hospital compensation, the financial burden can be outstanding.
Above the financial risks are the conscience risks. The majority of the regulations are in place to protect children from undue harm. Having a product that is not compliant can create an increased risk for safety issues. Do note that a compliant product does not necessarily mean a SAFE product. A product may be deemed compliant by following the required regulations, but simply may not be safe by design. For example, a new product design for a child’s bag may comply with the required lead levels, but may have studs that come off posing a laceration hazard (see the recall on children’s jeans March 7th, 2018).
How do you determine if the materials you’re using are compliant?
By reading the Code of Federal Regulations. Don’t worry, I’ve actually made it really easy and have created a couple of flow charts for those that make children’s products or clothing products.
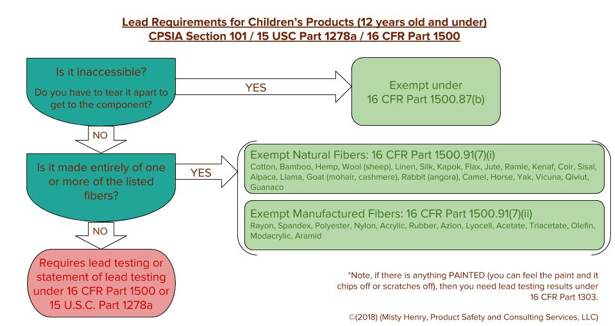
Typically, we are worried about lead (children’s products) and flammability (clothing products). For lead, pretty much any fabric without a painted design or non-fabric addition will be exempt from lab testing, aka, “compliant”. With flammability, we are looking at if it is raised (fuzzy like flannel, velour, fleece, terry, etc.) or if it is plain (knit, cotton woven, etc.). If it is raised, then we look at the fiber content. If it is made of one or any mix of polyester, nylon, acrylic, modacrylic, olefin, or wool, then it is exempt from lab testing. If it is plain, then it is exempt from lab testing no matter the fiber content.
If you are a registered small batch manufacturer, then if you have something that requires lead testing (for example), you can contact your supplier to see if it has already been tested and use their statement as your own. Keep in mind that lead and flammability are only two of the more needed tests that may be required of a product. Some tests depend on the finished product as a whole such as toys requiring “Use and Abuse” testing on the finished product. In the case of finished product testing, we cannot rely on a supplier’s statement.
How do you track components and finished products?
The hardest part is setting up a system that you love AND that works with your creative flow. You need basic information on your components and finished products and some of it actually overlaps with what you should be recording for your tax compliance needs.
Remember the ‘5 W’s’ from elementary/primary school? We are going to basically want to track that information: Where (or who) did you get it (from)? When did you get it? What is ‘it’?
If you are using a spreadsheet system, you’ll want to give it a reference code. Some components have a SKU or Style Number already and many utilize that for ease. The idea is that we can list the exact components (or ingredients!) in the finished product tracking. That is, we need to know that you used Material A purchased in May 2017 vs Material A purchased in August 2017. The finished product tracking notes what ‘it’ is, lists what components were used, when it was finished, and what code you put on the permanent tag (if required). The idea is that you are able to answer questions from just that code on the permanent tag, conduct a recall based on a component recall, and a customer will know if they are involved in a recall.
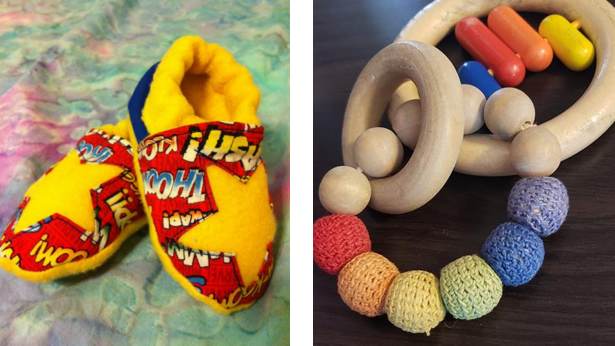
What type of labeling is needed for products?
This greatly depends on the product. All children’s items require Consumer Product Safety Commission’s (CPSC) tracking information for the manufacturer or private labeler name, city and state of production of the product, date of production, batch or run number, and “any other information to facilitate ascertaining the specific source of the product” like a website or email.
Clothing requires fiber content and care labeling from the Federal Trade Commission (FTC), country of origin from US Customs and Border Protection (USCBP), and, if it is for children, the tracking information. Toys should have age grading on the tag (0+, 0-6y, 14+, etc.) for CPSC compliance. Bath and body products should have an ingredient list to comply with CPSC or Food and Drug Administration (FDA) regulations.
What is a statement of compliance, and where should it be posted?
A statement of compliance is your official word that your product complies with the required CPSC regulations. You may also include any voluntary standards and/or required international regulations followed. This statement is created by you and can be done in a word processing program saved to your computer, cloud, and/or printed off as desired. This statement is only required to be accessible by retailers or any business reselling or redistributing your product and must be furnished to the CPSC immediately upon request.
You are not required to provide this document to a consumer, though a short statement indicating your compliance is always welcome; “Meets CPSC Safety Requirements” is official wording for labels and online listings. Note that only products directly under CPSC jurisdiction will be required to have a statement of compliance. Other agencies such as the FDA may not require such a statement to be kept in your records. For the CPSC-required statement of compliance, there are 7 parts that describe what the product is, what regulations it must abide by, who manufactures the product, who maintains records of compliance, when and where the product is manufactured, any testing done, and any exemptions from testing allowed.
Could you give examples of the type of testing needed for bath and body products? Jewelry? Handbags?
For some items, there won’t be any testing required. For example, adult handbags don’t actually require any testing under the CPSC nor do they require labeling under the FTC!
Children’s jewelry requires a number of heavy elements testing, but adult jewelry doesn’t. Bath and body testing depends on if it is covered under FDA or CPSC.
What concerns might a maker/handcrafter have that may be different than a business owner who has their product manufactured? What should each business owner look out for with product safety?
Both must follow the same steps; the difference between the two usually comes down to the eligibility of being a small batch manufacturer. Those who are eligible as small batch manufacturers can register and then utilize component part testing done by their suppliers for things like lead, flammability, and phthalates.
Those who import finished products typically are not eligible for this testing relief as they are not considered a small batch manufacturer due to the factory creating more than 7,500 units of that item in a year. When importing, I highly suggest watching testing reports very carefully. Many have come back as incomplete, outdated, or with incorrect test results. I always recommend spot testing at a lab every year or so to make sure things are still in compliance.
When having products manufactured domestically, it is like a middle ground between handcrafters and importers. Handcrafters have the benefit of being so familiar with their products and their customers, that tracking and recalling are usually simple and quick. When having larger amounts manufactured, tracking is a bit more tricky and recalls can be less effective. Even large companies complain about their recall efficiency! Once a product leaves your facility, you don’t have much control over what a consumer chooses to do, or not do, with it when faced with a recall decision.
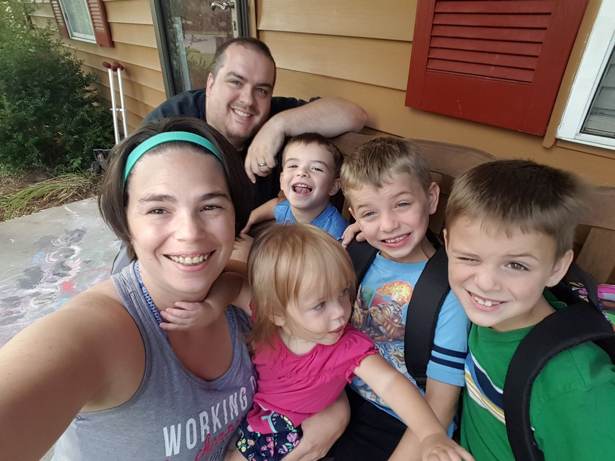
Misty Henry wakes up every day ready to encourage and support small businesses like yours so that every person has the tools they need to support their families the best way they can. To work closely with her, you can join one of her membership levels at MyProductSafety.com or join her Product Safety Course. If you aren’t quite ready to dive in with the added personal assistance, she offers digital mini-books and digital tracking templates to still provide you with the tools you need to succeed. If you have any questions you can always contact her at info@MyProductSafety.com. To follow Misty and her quick tips, you can find her on Facebook and Instagram.
A Newsletter That Goes Beyond Shopify 101
It’s easy to find beginner info about ecommerce online. If you’re past that? Subscribe to our newsletter for advanced strategies and need-to-know info for established shops. You'll get:
- Weekly tips to help you market and sell your products
- Updates when there is news that may impact your site
- Round ups of interesting links and info for brands
- Invites to our live trainings and webinars
- Instant access to our past emails
"*" indicates required fields
4 thoughts on “Consumer Product Safety Compliance For Small Businesses”
Leave a Comment
Related Posts
Let's take your online shop to the next level
The Shopify websites we design have a reputation for substantial improvements to ecommerce conversion rates and online sales. Let's talk!
This is really great info! I think it’s also important to note that these are the guidelines and requirements to sell products within the US only. Many countries have their own set of regulations that must be met if you are to sell to that country.
Good point, June! Thanks for stopping by!
There’s so much more involved than I first thought. So useful and informative, thanks!
I’m glad this was helpful, Sarah!